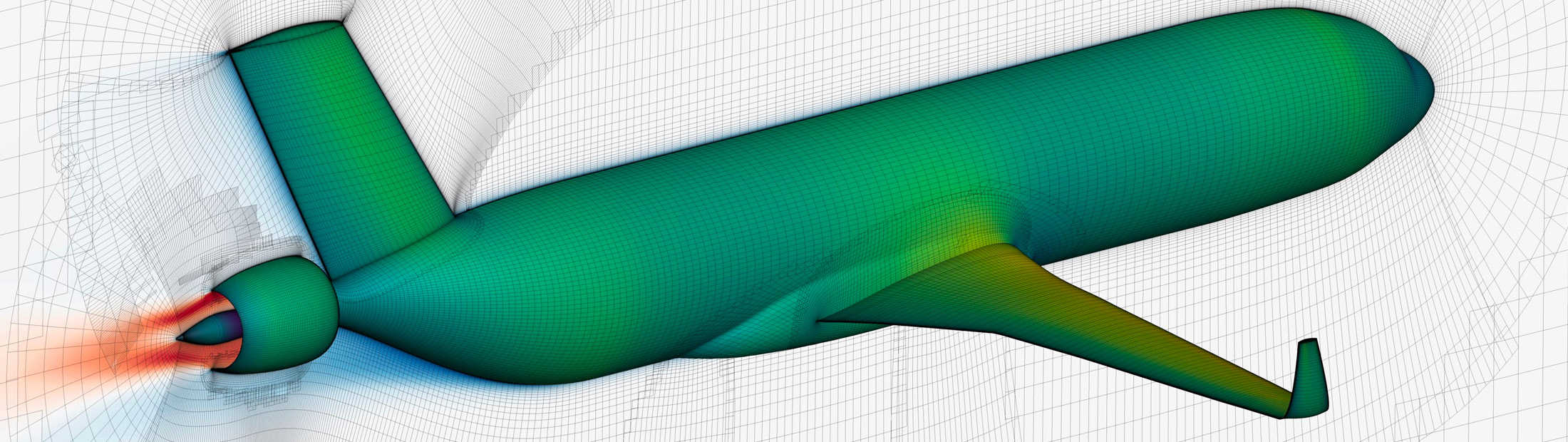
The need for innovations and cost reduction in aerospace engineering
Professor Joaquim Martins was featured in Aviation Week or his views on the next era of aviation and how we leverage model-based systems engineering to get there
Professor Joaquim Martins was featured in Aviation Week or his views on the next era of aviation and how we leverage model-based systems engineering to get there
Written by Joaquim R. R. A. Martins
The use of sophisticated digital models and powerful computer simulations, known as model-based systems engineering, is a step toward meeting both demands. Multidisciplinary design optimization can complement model-based systems engineering by making optimal decisions automatically until it finds the best design.
Designing a new aircraft involves thousands of decisions about shape, sizing, systems and operations. When making these decisions, engineers consider multiple disciplines such as aerodynamics, structures, propulsion and controls. The current engineering design approach performs sequential design tasks that mostly keep the engineers in discipline-specific silos to cope with complexity. Multi-disciplinary design optimization (MDO) expedites decision-making by automating the low-level decisions and addressing more of them earlier in the design cycle. MDO accomplishes this by using sophisticated algorithms that evaluate different designs and learn from data gathered from simulations to create a path toward the optimal design. The result is a design that is better than can be obtained through the conventional sequential design process. Also, addressing more requirements and interactions earlier in the design process mitigates costly redesign work.
Consider the design of an aircraft wing: How is a wing designed, and how can we improve the process? Traditionally, the conceptual design team decides on the wing area and span by considering the takeoff, landing and climb requirements while minimizing the overall operating cost. The structural wingbox layout is also typically defined at this point. After the area and span are fixed, a team of aerodynamicists designs the wing airfoil shapes with the help of computer-aided design and computational fluid dynamics (CFD). Once the shape of the wing is defined, structural designers size the wingbox elements. Most of the manufacturing process decisions are made after the fact, limiting the potential cost reductions at each step.
MDO provides a more holistic approach that moves the design decisions earlier in the design process and enables them to be made simultaneously. In the wing design example, that means optimizing the wing area, wingspan, airfoil shapes and structural sizing in a single design phase instead of multiple sequential phases.
Control systems for load alleviation could also be optimized in this single phase for further gains. In addition to making the decisions corresponding to multiple disciplines in a single phase, MDO uses computer algorithms to automatically find the best possible design by maximizing performance while satisfying requirements.
One obvious benefit of the MDO approach is that it reduces the design-cycle time and thus the research and development cost. The automatic optimization and simultaneous consideration of multiple disciplines achieve better design trades and, therefore, higher performance than the sequential siloed approach. Making more decisions and considering more requirements and disciplines up front reduces risk and cost. For example, assessing more detailed simulations of the wing response to gusts early on can find issues that would otherwise be found later and require costly structural reinforcements. The cost can be further reduced by simultaneously optimizing the wing design and its manufacturing process.
Given the benefits of the MDO approach, why have we not seen it used more widely in the aerospace industry? One reason is inertia: Changing the status quo requires significant investment and is not without risk. Startup companies can create a more efficient research and development process that includes MDO because they are not hampered by an existing design workflow. More broadly, the industry can leverage investment in model-based systems engineering (MBSE) to implement MDO as part of the design cycle because both MBSE and MDO require computational models and a digital thread. MDO would automate and thus speed up many of the steps within the MBSE process.
MDO is not a panacea. We still require human engineering intuition. Just as the advent of CFD simulations did not replace aerodynamicists, MDO is not replacing engineering designers. Instead, it relies on engineers who are well versed in computer simulations and numerical optimization. MDO allows engineers to spend less time on detailed design and more time considering the system requirements. With MDO, we need not settle for merely improved designs—we can consistently find the best ones.
Click here to read the original article in Aviation Week.