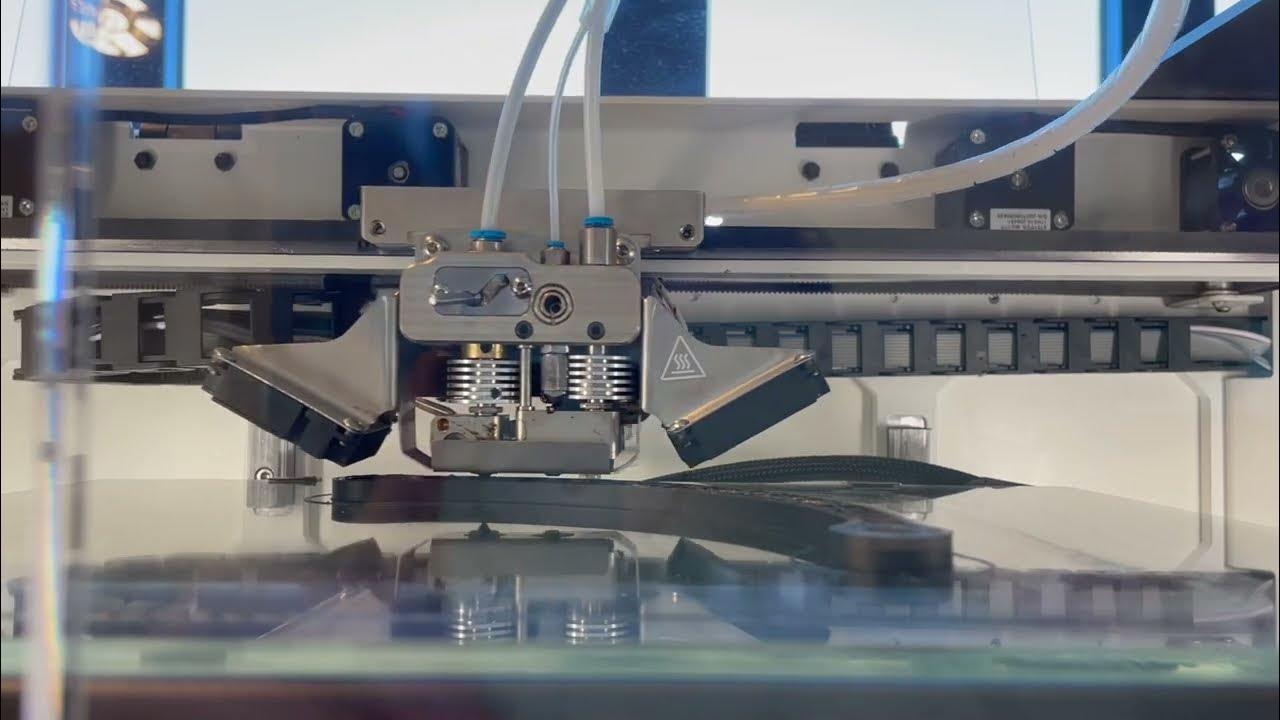
Faculty Profile: Anthony M. Waas
A look into Aerospace’s Department Chair’s research.
A look into Aerospace’s Department Chair’s research.
How do you manufacture solar arrays in space? What is the strongest, lightest airplane wing material to withstand years of use without failure? And how do you predict its lifetime?
These are questions pursued by Anthony M. Waas, faculty member and department chair of the University of Michigan Aerospace Engineering department.
Waas joined U-M in 1988 as an Assistant Professor in the Department of Aerospace. 30 years later he became the Richard A. Auhll Department Chair after an astounding career that continues to impress, innovate and inspire.
As the head of the University of Michigan Composite Structures Lab (CSL), his aim is to create aerospace structures made of carbon fiber reinforced plastic, which is the same material used in tennis rackets. Composite structures are very stiff and very light, which would allow for the weight of an airplane to be minimized and therefore make it ideal for fully loaded cargo. The need to reduce the cost of production and certification cost of flying vehicles is more urgent than ever; therefore, the possibility of increasing automated manufacturing of large aerospace structures, and developing validated, robust digital tools for certifying aerospace structures made of composite materials are groundbreaking.
To achieve this goal, his team (which includes several faculty and students from Aero, as well as colleagues from a variety of other departments at Michigan) performs a combination of experiments, computational modeling and analysis, and theoretical developments when necessary.
Waas’ research currently revolves around lightweight multi-materials structures (MMSs). These structures include continuous fiber reinforced laminates, textile laminates, ceramic matrix composites for high temperature applications, layered materials, sandwich structures with a variety of cores, and nanoparticle reinforced polymers, which all require advanced analysis tools for characterizing their mechanical, thermal, and electrical behavior. Dr. Waas’ goal is to develop validated analytical and computational methods to understand how a structure (such as an aircraft) made of MMSs responds to external environments, including understanding how they damage and fail.
Modeling is the common thread of his research over the decades. For the last 30 years, Waas has worked on different types of composites and predictive models for them. “When you are in an airplane, you don’t want to think about the fatigue load of the aircraft – the daily wear and tear over the airplane’s lifetime. Predicting failure to develop the most efficient, stable behavior from the materials that comprise the aircraft is essential.”
Composite failure is critical in aircraft carbon fiber to predict performance and safety for a specific number of cycles. Modeling simulations are the key, and Waas points to computer modeling predictions as an essential research tool to decrease the cost and time for structural enhancements.
And it’s a moving target, as new, lighter composites are developed, and as aircraft change in shape and complexity with the development of sustainable alternative fuels. The team explores different types of carbon fiber laminates, glass fiber braids, textiles, and twill composites, all of which can be laminated, braided, or woven, depending on the application and composite need. Finding the right materials and form for specific uses is the sweet spot of an efficient, lightweight, lasting structure.
Dr. Waas dedicated his Ph.D. to studying how carbon fiber reinforced plastic structural components carry compressive loads. “To design a good airplane,” he said, “you need to understand how these materials will behave, but also how they will break.” Therefore, Dr. Waas acts not only as an engineer but also as a physicist, writing the equations that will govern the deformation response of these composites where they are to be used in airplanes and spacecraft, and then innovating with ways to improve them even further.
Carbon fiber is a man-made material; as such, its creation process differs enormously from working with metals. One of its main differences– and great benefits– is that it can be used for 3D printing and acreage automated manufacturing.
These structures have been 3D printed. Apart from looking aesthetically good, they have been specifically designed to (a) failure at higher loads by stiffness tailoring, (b) absorb large amounts of deformation energy. It is from designs like these that innovations for lightweight flying objects such as air taxis can start to occur. “If you design the floor of the air taxi with a passive energy absorbing structure, then when it hits the ground it will fail gracefully due to the “smart” base absorbing significant amounts of crush energy from the impact. That prevents the whole structure from disintegrating,” Dr. Waas explained.
Dr. Waas is working with students at the U-M Stamps School of Art and Design to produce these 3D designs. Origami inspired structures show unique ways structures can be designed for different applications, including eVTOL and deployable structures for space manufacturing.
Waas continues, “Most space structures are foldable, taken up in space, and deployed. Origami makes sense to develop new concepts and helps our lab consider new shapes and forms and analyze these structures. I want to learn how these students think. They consider the shape and form differently than an engineer does, and I want to understand how I can use that to incorporate new ideas into my structural designs.”
Stamps students who are interested in aerospace structures and materials can take courses that will teach them how a structure like the ones above will deform. This will allow them to analyze them and produce better, safer, and cooler designs.
“The students I work with may not know much about the analysis of the structure, but they know what’s aesthetically pleasing,” Dr Waas said. “I really enjoy working with these students and other colleagues to advance research by teaching them about deformable structures and learning from them about shape and form.”
Dr. Waas is also currently working with the engineers at Boeing, Lockheed Martin, and Toyota North America to design safe hydrogen tanks. Although hydrogen is already being used as a way to propel cars, such as in the Toyota Mirai, Dr. Waas is working on a way to safely store hydrogen for propelling vehicles. He’s researching a pressure vessel made out of carbon fiber composites that can store large volumes of compressed gaseous or liquid hydrogen.
Regarding his work in aerospace, Dr. Waas looks forward to someday working with companies that can accelerate the insertion of cool products into a vehicle in a safe but efficient manner.
A recently renewed DARPA project is pursuing solutions for additive manufacturing in space, 3D printing components in space and modularly assembling them, using different thin-walled structures and wall thicknesses to develop practical space manufacturing applications that stand up to intense environments. Working with researchers across engineering disciplines, the project objective for the eight selected university teams would enable large structures like solar arrays, antennas, and optical systems to be built in orbit for orbital applications. Leading a vibrant lab in pursuit of materials and applications never done before, Waas is excited by all of the things his team is doing. “Aerospace engineering is cutting edge and dynamic. New things emerge continuously which makes aerostructure design a very exciting career path. I can’t wait to see what we do next!”