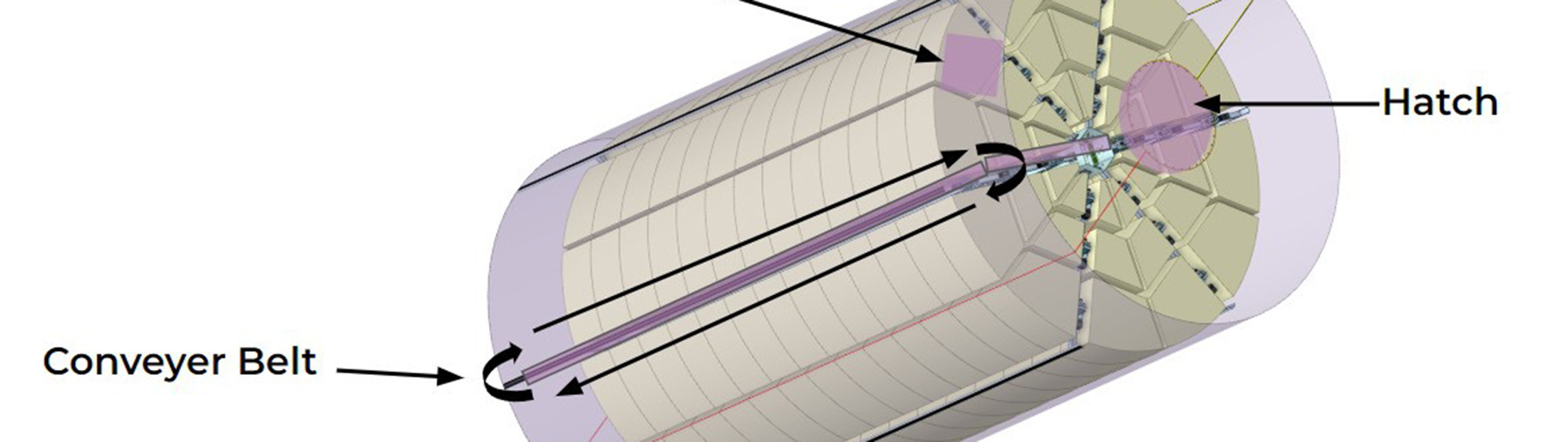
Vending Machines in Space
Building a cargo recovery system for the Lunar Gateway space station on the moon
Building a cargo recovery system for the Lunar Gateway space station on the moon
Finding a tape measure in the junk drawer is nothing compared to the complex matrix of stored gear in confined spaces like the International Space Station. You know it’s in there, but the process of finding and digging it out takes a while and can make a mess.
Enter the Autonomous Cargo Management & Distribution project team in the Model-Based Systems Engineering course series, who is developing a prototype system for NASA to make it easier to find and retrieve gear in space.
The team is competing in Moon to Mars eXploration Systems and Habitation, or X-Hab, an annual NASA academic innovation challenge. As a part of X-Hab, the group of students in the x88 MBSE courses developed the Autonomous Cargo Management System from cradle to grave. The intent of their system is to revolutionize the organization and retrieval process for cargo in the Lunar Gateway–a future space station, like the ISS for the Moon.
Cargo retrieval in the ISS is currently an excruciating process, taking ten minutes on average to scavenge an item from a nesting-doll-like system of bags and boxes. Adding to the challenge is the tricky volume utilization within logistics modules in the ISS.
How it works
“It’s a cheese wheel,” says team lead Owen Faulkner.
Faulkner and his classmates in the X88 program are also part of BLiSS, or the Bioastronautics and Life Support System team, which works on a number of different projects in and out of the classroom.
“Cargo boxes of three set sizes, like USPS packages, hold a Dragon XL capsule full of logistics. These containers are attached to chains that motion axially along the capsule and summit requested cargo to the apex of a chain track within a meter of the capsule hatch,” explains Faulkner.
Essentially, the team designed a movable crane on a cross track that can identify and retrieve stored cargo for different cargo sizes and weights, and operate in environments ranging from microgravity to 1g. Other key aspects critical to the space environment include using radio frequency identification chips to autonomously identify cargo and develop it all in a lightweight, space-conscious way to enhance modular assembly.
Continual Reviews
The team undergoes a series of design reviews during the year, presenting to and receiving feedback directly from engineers and executives from leading aerospace organizations, including any sponsoring companies (the lab has attracted many industry funders). The design reviews increase in scope and complexity as the team evolves their product. The end review is not surprisingly called the Flight Readiness Review (FRR), which leads to a ‘go or no go’ assessment of the project.
For this team, it’s a go. And they are literally going.
A great invitation
NASA wants to see up close what U-M students have designed. The team is traveling to Cape Canaveral to share their design specifications in person, bringing with them two demonstrative prototypes: the Operational mock-up is a half-scale slice of the system whose purpose is to demonstrate the novel motion of the system, while the Ergonomic mock-up is a full scale slice of the system whose purpose is to demonstrate the user interaction in cargo retrieval and return.
Faculty lead of the MBSE program George Halow isn’t surprised about this trip. “These students have been beyond impressive every step of the way. They’ve blown us out of the water at every design review. They’ve mastered advanced systems engineering concepts to create a prototype model and present their findings repeatedly to a c-suite audience. That’s part of the class here, but the level at which they’ve done it is a testament to their capabilities.”